In this article, we will explore the key types of industrial robots that are revolutionizing factory and warehouse operations. From Cartesian Robots to SCARA Robots, Articulated Robots to Delta Robots, each type offers unique features and advantages, enabling manufacturers to choose the most suitable option for their specific needs. Join us as we delve deeper into the capabilities and benefits of these industrial robots and their impact on the manufacturing landscape.
Key Takeaways
- Cartesian Robots, SCARA Robots, Articulated Robots, Cylindrical Robots, and Delta Robots are all types of industrial robots.
- Each type of robot has its own unique features and advantages.
- The choice of robot type depends on the specific application requirements, workspace constraints, and desired capabilities.
- Some common applications of robotics in industrial automation include CNC machines, 3D printing, assembly, welding, material handling, packaging, and pick-and-place operations.
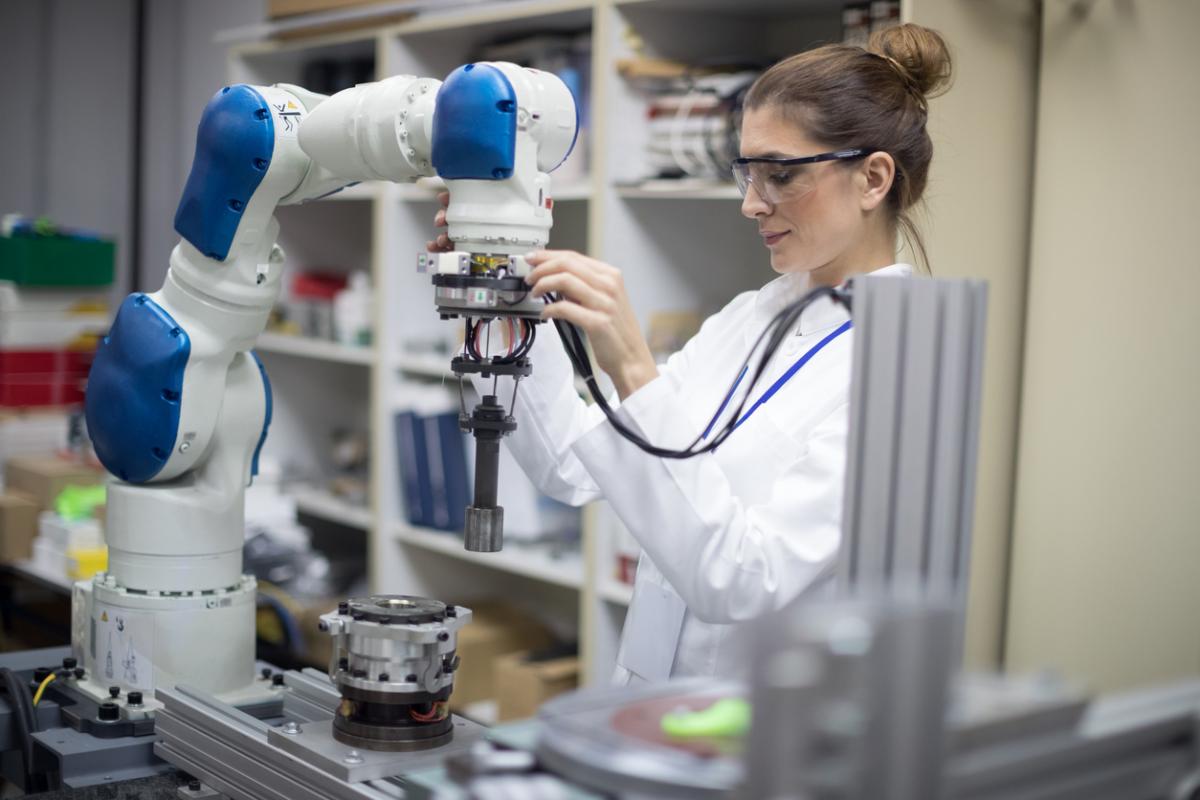
Different types of industrial robots
Different types of industrial robots exist to cater to the diverse needs and requirements of various industrial applications, ultimately boosting manufacturing productivity. Each type of robot has its unique advantages and features that make it suitable for specific tasks. The range of motion, control, and safety measures vary across the different types of robots.
Articulated Robots
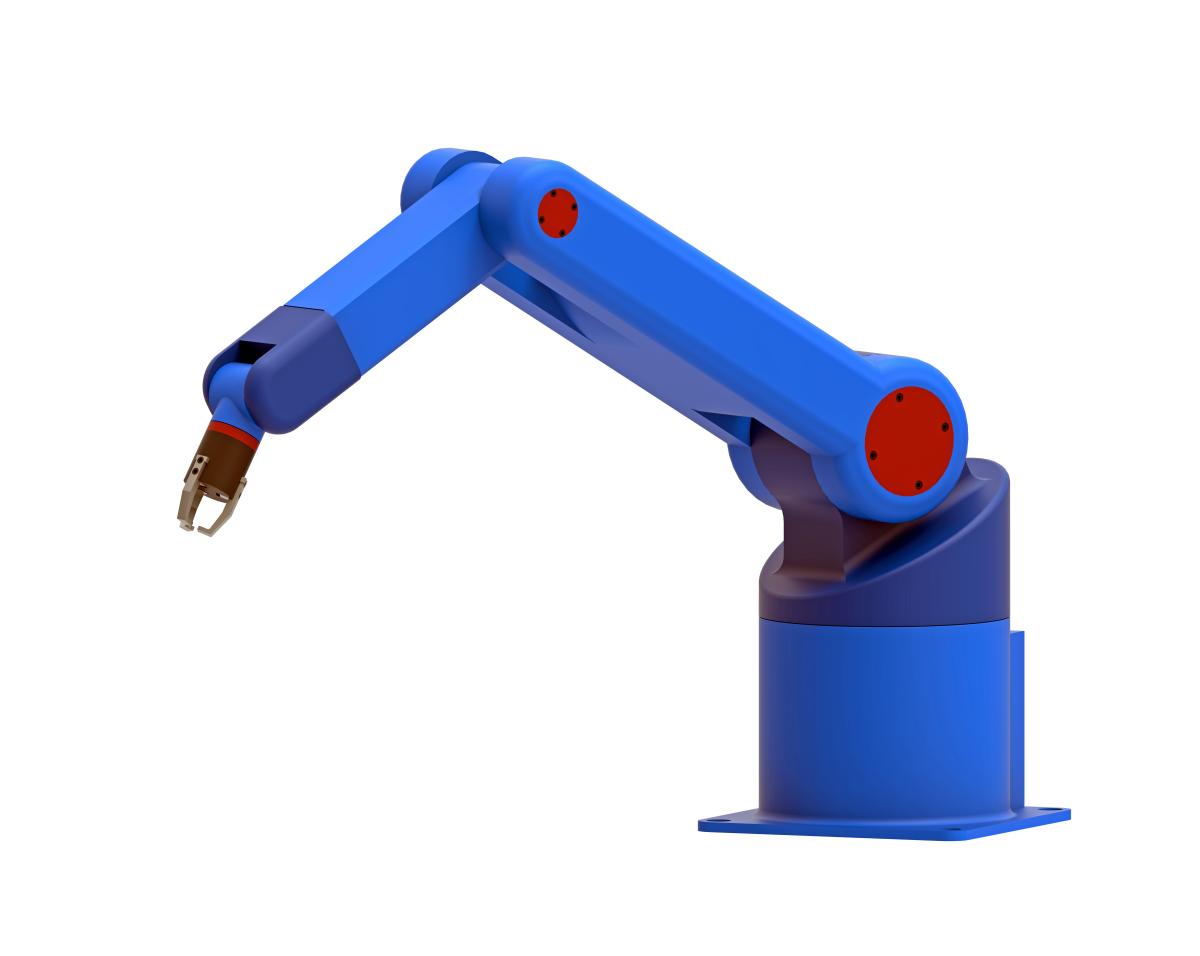
Articulated robots, also known as 6-axis robots, are widely used in industrial manufacturing for their flexibility and precise movement capabilities. These robots have a mechanical movement and configuration that resemble a human arm. They are mounted to a base with twisting joints and can feature two to ten rotary joints, allowing for greater motion. The joints of articulated robots can be parallel or orthogonal to each other, providing different degrees of freedom.
The flexibility of articulated robots makes them suitable for a variety of industrial applications such as assembly, arc welding, material handling, machine tending, and packaging. They can perform complex operations with high precision, making them ideal for tasks that require intricate movements and accurate positioning.
The rotary joints in articulated robots enable them to move in multiple directions, mimicking the versatility of human arms. This enables them to access hard-to-reach areas and perform tasks in confined spaces. Articulated robots’ precise movement capabilities contribute to increased efficiency and productivity in manufacturing processes.
Cartesian Robots
Cartesian robots, also known as linear robots or gantry robots, contribute significantly to manufacturing productivity. These robots utilize a Cartesian Coordinate system with three linear axes (X, Y, and Z) to achieve precise and controlled movements. The linear movement capability of Cartesian robots makes them well-suited for a wide range of assembly applications in various manufacturing sectors.
Cartesian robots are highly flexible in their configurations, allowing for adjustments in speed, precision, stroke length, and size. Their simple design and operation make them affordable and easy to integrate into existing production lines. However, they do require more space compared to other robot types and have limitations in terms of speed and acceleration.
One of the common applications of Cartesian robots is in CNC machines, where they provide precise and efficient control over the movement of cutting tools. They are also widely used in 3D printing, where their precise linear movements enable the creation of complex and intricate structures.
Cylindrical Robots
Moving on to another key type of industrial robot that contributes to manufacturing productivity, we have cylindrical robots. Cylindrical robots are characterized by their rotary joint at the base and a prismatic joint to connect the links, resulting in a cylindrical-shaped work envelope. These robots are commonly used in tight workspaces for simple assembly, machine tending, or coating applications. One of the main advantages of cylindrical robots is their compact design, which allows them to operate effectively in confined spaces.
Cylindrical robots are known for their high load-carrying capacity, making them suitable for various manufacturing tasks such as welding automation, material handling, assembly operations, and painting. Despite their ability to handle heavy loads, cylindrical robots take up more space compared to other industrial robot types. However, their efficiency and versatility in performing tasks compensate for this limitation.
Delta Robots
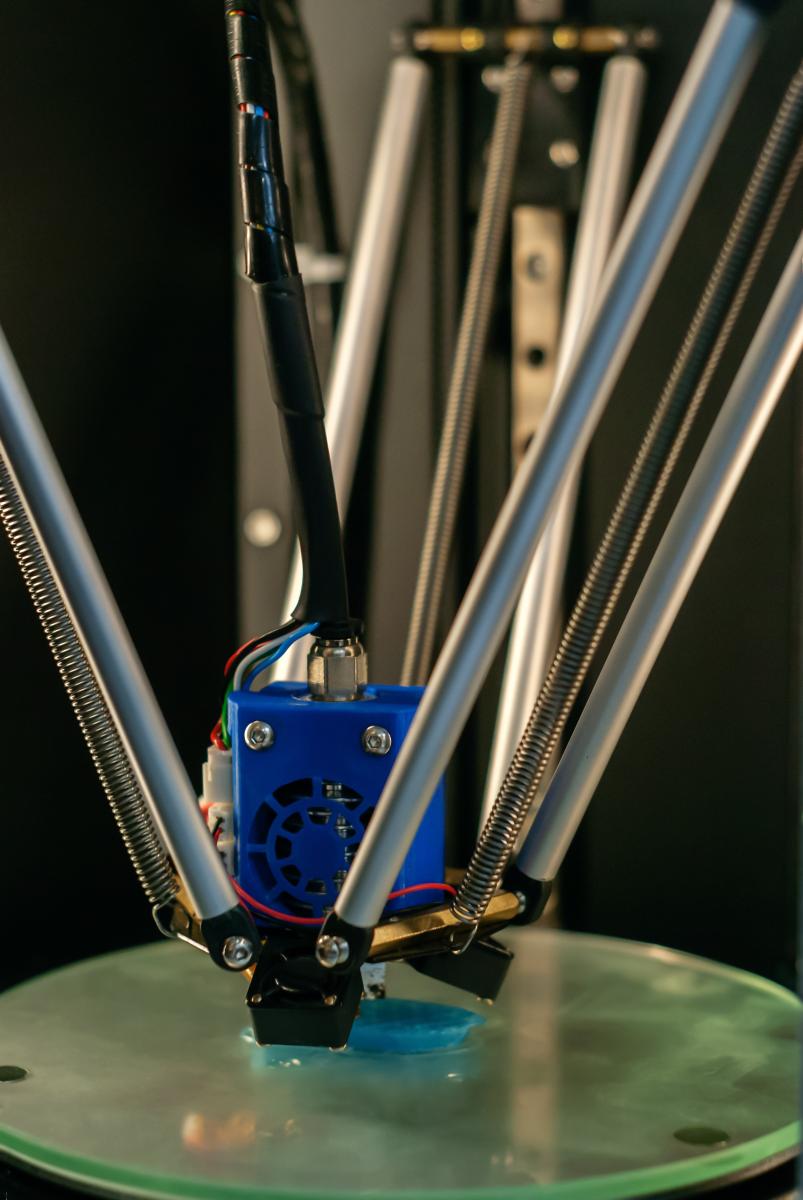
Delta Robots are parallel robots that feature three arms connected to a single base. They are highly efficient and widely used in industries to boost manufacturing productivity. Here are four key points about Delta Robots:
- Fast and Precise: Delta Robots are known for their high-speed operation and precise motion control. They can perform fast pick and place applications with great accuracy, making them ideal for industries such as food, pharmaceutical, and electronics.
- High Payload Capacity: Despite their compact size and minimal floor space requirement, Delta Robots have a high payload capacity. This allows them to handle heavy objects during production processes, further enhancing manufacturing productivity.
- Limited Workspace: Delta Robots have a dome-shaped work envelope, which means their range of motion is limited compared to other industrial robot types. However, their speed and precision compensate for this limitation, making them a preferred choice for specific applications.
- Pick-and-Place Applications: Delta Robots are commonly used for pick-and-place tasks, where they efficiently transfer products from one location to another. This makes them invaluable in assembly lines, packaging, and various other manufacturing processes.
SCARA Robots

SCARA Robots have emerged as a significant contributor to manufacturing productivity in recent years. These robots, which stand for Selective Compliance Assembly Robot Arm, are known for their fast and accurate movements, making them ideal for assembly, pick-and-place, and packaging applications. SCARA Robots have a compact design, allowing them to fit into tight workspaces without sacrificing performance.
The main advantage of SCARA Robots is their ability to perform lateral movements. With two parallel joints providing compliance in one selected plane, SCARA Robots can easily maneuver and manipulate objects with precision. This makes them highly efficient in assembly tasks, where speed and accuracy are crucial.
In the industrial sector, SCARA Robots have played a vital role in boosting manufacturing productivity. Their fast and accurate movements allow for faster production cycles, reducing cycle times and increasing overall output. Furthermore, their compact design enables manufacturers to optimize their workspace and maximize production capacity.
Collaborative Robots
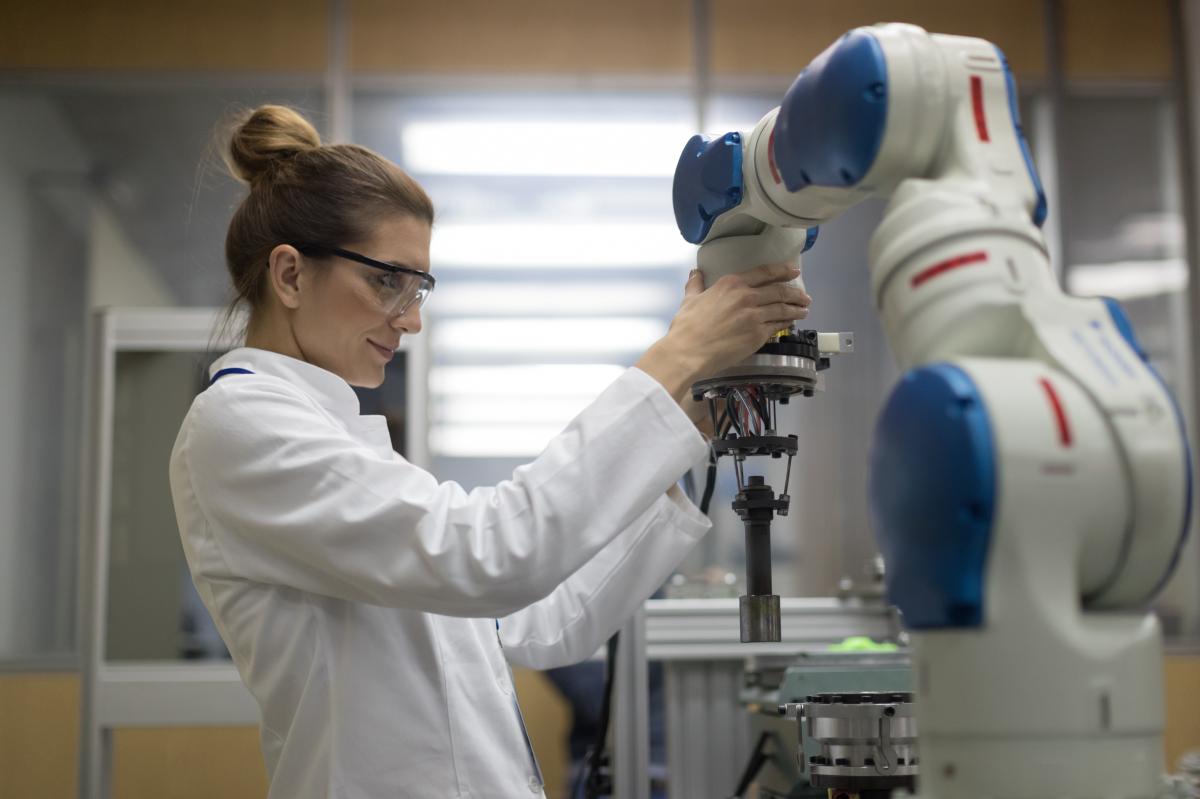
Collaborative robots, also known as cobots, are an important category of industrial robots that facilitate safe and efficient collaboration between humans and machines in manufacturing environments. These robots are specifically designed to work alongside human workers, assisting them in various tasks and boosting overall manufacturing productivity. Unlike traditional industrial robots that are typically caged off from human workers, collaborative robots are equipped with advanced safety features that allow them to operate in close proximity to humans without posing a danger to their well-being.
The key advantage of collaborative robots is their ability to enhance human-machine interaction, enabling seamless cooperation in tasks such as assembly, pick-and-place operations, and small-scale manufacturing. They are easy to program and operate, making them accessible to workers without extensive robotics expertise. Collaborative robots can contribute to increased efficiency and flexibility in production processes, as they can handle repetitive or physically demanding tasks, while leaving more complex decision-making and problem-solving to human workers.
Serial Manipulators
Serial manipulators are a common type of industrial robot that features motor-actuated joints connecting its links. These robots, also known as articulated robot arms, play a crucial role in boosting manufacturing productivity. Here are four key points to understand about serial manipulators:
- Versatile and Flexible: Serial manipulators have a wide range of motion and can perform complex tasks with precision. They are capable of reaching various points in their workspace, making them suitable for applications such as assembly, welding, material handling, and packaging.
- Six-Axis Robots: Most serial manipulators are six-axis robots, meaning they have six degrees of freedom. This allows them to move and rotate in multiple directions, providing increased flexibility and the ability to perform intricate tasks.
- Linkage Design: Serial manipulators consist of a series of links connected by motor-actuated joints. These joints enable the robot to move its links independently or in coordination to perform specific tasks.
- Advantages over Parallel Robots: While parallel robots offer better rigidity, serial manipulators have the advantage of longer reach, higher payload capacity, and a greater range of motion. They are also easier to program and operate, making them more versatile in manufacturing environments.
Parallel Manipulators
One type of industrial robot that plays a significant role in boosting manufacturing productivity is the parallel manipulator. Parallel manipulators, also known as parallel link robots, are designed with a system of parallel linkages that connect the end effector or tool to the base. These robots are capable of performing a wide range of tasks due to their unique design.
The parallel manipulator consists of multiple rotational joints that enable precise and coordinated movements. This allows the robot to carry out tasks such as assembly operations, pick-and-place operations, and various other operations that require accurate positioning and manipulation.
One advantage of parallel manipulators is their high rigidity, which ensures stability and repeatability in their motions. This makes them particularly suitable for tasks that involve heavy loads or require high precision.
Lower Mobility Manipulators
Lower Mobility Manipulators play a crucial role in enhancing manufacturing productivity by providing precise and efficient robotic solutions for various industrial applications. These manipulators have a lower number of degrees of freedom compared to other types of industrial robots, which makes them advantageous for simpler architectures and faster motion. Here are four key aspects of lower mobility manipulators:
- Lateral Movements: Lower mobility manipulators excel in lateral movements, allowing them to perform tasks that require precise motion in the horizontal plane. This makes them ideal for applications such as assembly, where parts need to be accurately positioned and joined together.
- Cartesian Coordinate: Lower mobility manipulators often operate on a Cartesian coordinate system, utilizing linear robots that move along three linear axes (X, Y, and Z). This allows for precise positioning and control, ensuring accurate and repeatable movements.
- Safety: Lower mobility manipulators are designed with safety in mind. They are equipped with advanced sensors and safety features to ensure the protection of human operators and prevent accidents in the workplace.
- Applications: Lower mobility manipulators find applications in various industries, including the automotive industry for tasks such as welding and assembly, as well as in injection molding for precise material handling and part manipulation.